CARIMA X1によるエレキギターのボディ製作

~高速・高精度造形が実用パーツを可能にする~
カスタム製作やプロトタイプ、小ロット試作に最適な3Dプリンターとして注目を集める「CARIMA X1」。
今回はその実力を検証するため、実寸大のエレキギターのボディをフルスケールで造形してみました。
本記事では、造形プロセスや仕上がりの精度、そしてX1ならではの特長について詳しくご紹介します。
目的:
一点モノの実用パーツ製作にX1は使用可能かを検証する
量産とは異なり、一点モノやカスタム製作では手間やコストが大きな課題です。特にエレキギターのボディ製作は複雑な形状もあり、試作のハードルが高い領域。
しかし、3Dプリンターでの造形が可能になれば――
- 設計変更の迅速な反映
- 複数パターンの試作対応
- デザインの自由度拡大
といった多くのメリットが期待できます。
そこで、今回は大型の造形が可能であるCARIMA X1を用いてエレキギターのボディを造形し、
サイズの大きい一点モノパーツやカスタムパーツの製作に適用できるのかを検証していきます!
今回の検証のポイント
実寸サイズでの大型造形が可能か?
ギターサイズ:X:325mm Y:44.5mm Z:460mm
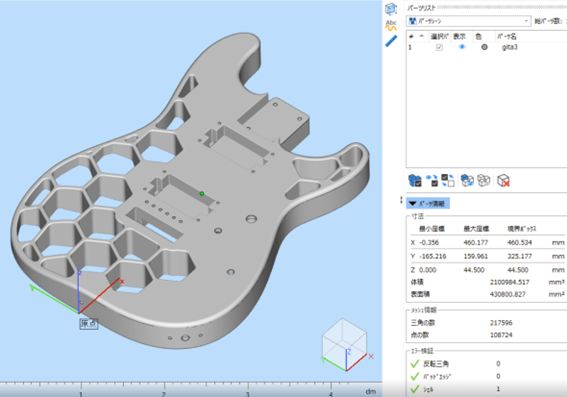
造形環境と使用データ
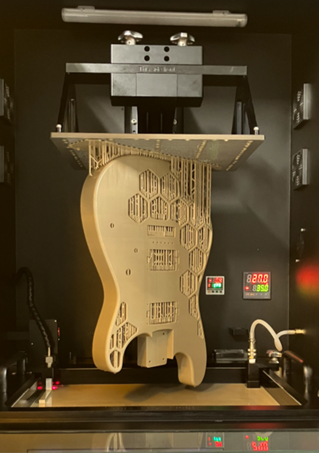
使用機器 | CARIMA X1 (DLP方式/405nm) |
材料 | 高剛性・耐衝撃性レジン (岩間工業所取り扱い) |
積層ピッチ | 0.1mm |
出力時間 | 約16時間 |
サポート・配置 | CHITUBOX Pro for CARIMA |
出力後、IPAで洗浄し、サポートの除去と表面仕上げを行いました。
UVによる二次硬化は、寸法の安定性と強度を確保するための重要なプロセスです。
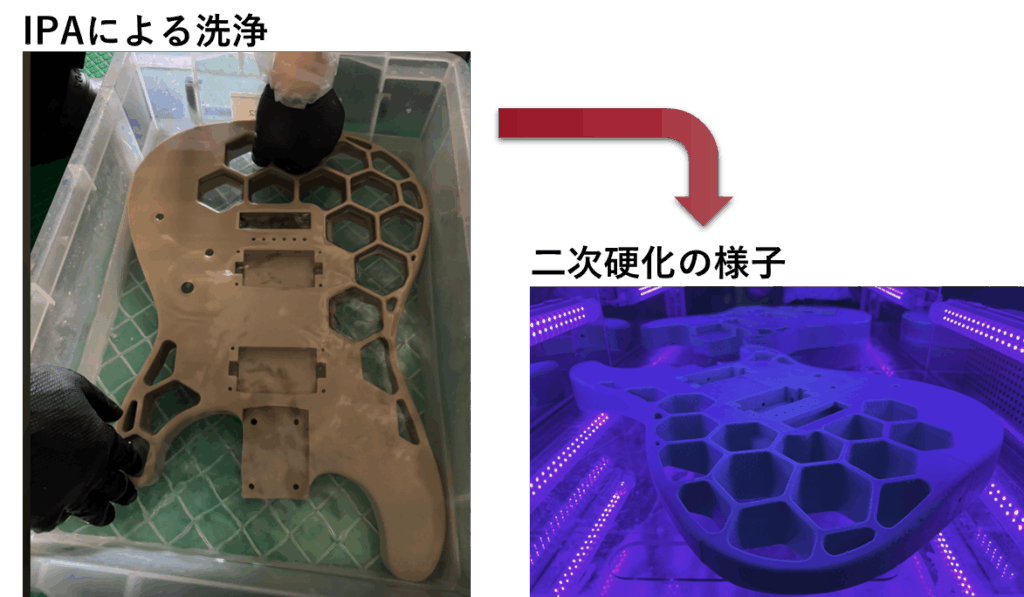
検証結果:
大型サイズも安定・高速・高精度な造形が可能!
造形中は反りや積層ズレもなく出力成功。
細かいディテール(ネックポケットやピックアップキャビティ)も再現度が高く、そのまま実用可能なレベルでした。
また、オープンマテリアル対応の強みを活かし、実際にネジ固定・ピックアップの取り付けにも十分な強度が確保されていることが確認できました。
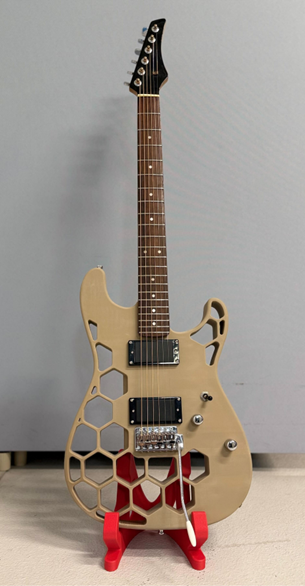
X1を選ぶ理由:アイデアから実物へ、”即戦力”としての3Dプリンター
CARIMA X1の強みは、以下の3点に集約されます:
● テンションフリーフィルムの採用
剥離力がほとんどなく、大型造形でも造形トラブルを抑制。
● 最大クラスの造形エリア
ギターボディのような大型構造物もワンショットで出力可能。
● オープンマテリアル対応
材料選定の自由度が高く、試作から実用品製作まで幅広く対応。
一点モノでも、プロトタイプでも、即実用できるパーツを高速・高精度で。
CARIMA X1は、アイデアを“かたち”に変える頼れるパートナーです。
ご質問やデモ、実機見学のご希望は、ぜひお気軽にお問い合わせください。
お問い合わせはこちらから
info-3dsr@iwama-me.co.jp
製品詳細はこちらより